When it comes to industrial burners, there are only a handful of companies that have been working on them as long as us. This white paper provides a comprehensive guide to industrial burner systems. Covering how they work, how to maximize combustion efficiency, ensure safety, and evaluate upgrades or replacements.
Basics of Industrial Burners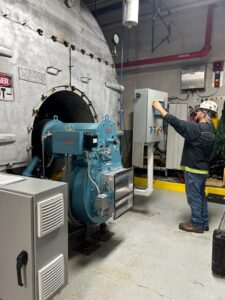
An industrial burner’s job is to mix fuel and air in the correct proportion for efficient combustion. The ideal mixture is known as a stoichiometric fuel-to-air mix. That just enough air to completely burn the fuel without any extra air added.
In practice however, burners must operate with excess air to ensure complete combustion and safety. Too much excess air though, wastes energy heating nitrogen and unused oxygen that go out the stack. In fact, every 1% of O₂ above the optimal level in flue gas wastes roughly 1% of fuel. Not to mention it also increasing emissions of NOx and CO. Conversely, too little air causes incomplete combustion (soot, unburned fuel, carbon monoxide).
Selecting the Right Industrial Burner (New or Retrofit)
Choosing an industrial burner—whether for a new system or retrofit—requires balancing performance, emissions, and installation needs. Here are the core factors to consider:
1. Capacity and Turndown Ratio Make sure the burner’s BTU/hr rating matches or slightly exceeds your boiler’s max firing rate. Undersized burners limit output; oversized ones may short-cycle. Turndown ratio is also key. Higher turndown (e.g., 8:1 or 10:1) is useful for fluctuating loads, but overly high turndown can compromise combustion stability or increase cost and complexity.
2. Fuel Type and Flexibility Burners are typically optimized for a primary fuel (natural gas, oil, biogas, etc.). If dual-fuel or backup is required, ensure the burner and fuel train are designed for it. Consider atomization for oil, and emissions differences between fuels.
3. Emissions Guarantees If your facility must meet specific NOx or CO limits, choose a burner with verified low-emission performance across the firing range. Low-NOx or ultra-low-NOx burners may require features like flue gas recirculation (FGR), which also affects fan sizing and controls.
4. Burner Controls and Efficiency Features Modern burners should include linkageless controls (parallel positioning), O₂ trim, and optional VFDs for the combustion air fan. These improve fuel efficiency, reduce electrical load, and allow precise modulation. Ensure controls can integrate with your plant’s BAS, PLC, or lead-lag systems.
5. Lifecycle Cost and ROI Don’t base decisions on upfront cost alone. Even a 3% gain in efficiency can translate to six-figure annual savings on a large boiler. Run the numbers or consult a burner specialist to compare long-term value.
Industrial Burner Components and Safety Systems
Industrial burners rely on several integrated systems to ensure safe, efficient combustion:
-
Fuel Train: Delivers fuel via pumps, regulators, valves, and safety shut-offs. Gas systems often include dual shut-off valves with a vent for leak protection and pressure switches to monitor safe ranges. Keep spare rebuild kits and switches on hand for quick fixes.
- Air System: A forced-draft fan supplies combustion air, regulated by dampers or VFD-driven motors. Airflow switches confirm purge and firing air is sufficient. A failed blower or blocked intake should trigger an immediate lockout.
- Ignition System: Uses a high-voltage spark or ignition electrode to light a pilot flame, which in turn ignites the main flame. Components like electrodes and pilot valves should be maintained, as ignition failures cause burner shutdowns.
- Flame Scanner: Detects flame presence using flame rods, UV, or IR sensors. If the flame goes out or isn’t detected, the burner shuts down to prevent unsafe conditions.
- Flame Safeguard: Acts as the safety gatekeeper. This system (often a BMS) enforces the startup sequence and shuts down the burner instantly if flame loss or unsafe conditions occur.
- Combustion Controls: Regulate firing rate and air-fuel ratio. Modern systems use servo motors and linkageless controls for precise modulation, often with digital interfaces, O₂ trim, and integration into plant automation (PLC/BAS). They include built-in safety interlocks for key conditions like high pressure or low water.
Combustion Efficiency Factors
-
Excess Air (O₂): Most boilers target about 3% O₂ in flue gas at high fire (~15% excess air). Well-designed gas burners can run with as low as 10% excess air (2% O₂) under ideal conditions. If your stack O₂ is creeping toward 5–8% at low fire, you’re likely wasting fuel and money. A rule of thumb from the U.S. Department of Energy is that boiler efficiency improves 1% for each 15% reduction in excess air.
- Stack Temperature: Higher exhaust temperatures mean heat is escaping. Each 40°F reduction in stack temperature can gain 1% boiler efficiency. Maintaining a proper air-fuel ratio helps keep stack temps in check.
- Complete Combustion: Inadequate air or poor mixing leads to soot, smoke, and CO. For example, 1 cubic foot of natural gas theoretically needs about 10 cubic feet of air for perfect combustion. However burners are typically sized to supply 12.5 cubic feet (or 25% extra) to ensure a complete burn. If air is too restricted, flame carbon monoxide rises and efficiency plummets.
Monitorin combustion effiecency involves measuring flue gas composition. A flue gas analyzer checks O₂, CO, and sometimes CO₂ levels to indicate how well the burner is tuned. Facilities with large fuel usage (>$50k/year) are advised to continuously monitor flue oxygen and excess air. By keeping excess air near the optimal point, you minimize losses up the stack and maximize heat converted to steam or process needs.
O₂ Trim: Maintaining the Perfect Mix Automatically
An O₂ trim system continuously measures oxygen in the flue gas and adjusts the burner’s air input to hold a target O₂ level . It acts as a “supervisor” on top of the base burner settings. If O₂ starts to rise (too much air), the trim system will slightly close the air damper or slow the fan to reduce airflow. If O₂ drops (too little air), it will open up to add air . These micro-adjustments occur every few seconds to compensate for changes in load, fuel quality, or barometric conditions . The result is the burner stays locked on its optimal air-fuel ratio at all times, without drifting.
O₂ trim systems can significantly benefit boilers that have widely varying loads or seasons . Plants report fuel savings on the order of 2–4% for natural gas (even 4–5% for oil) by tightening up excess air . Emissions of NOx and CO can also drop by up to 5% . Steam pressure control often improves (e.g. holding ±1 psi instead of wider swings) because combustion is more consistent . Less excess air also means less heat loss and less formation of thermal NOx, helping meet emission permits.
The U.S. Department of Energy recommends considering automatic O₂ trim on any large boiler burning over $50,000 in fuel annually . Many newer burner management systems come with O₂ trim as an option. They can also retrofit 02 trim on an existing system. You can accomplish this by adding a zirconia O₂ sensor, a controller module, and a VFD on the combustion air damper.
Low-NOx Performance
Running with minimal excess air helps limit both CO and NOx. Too much air can increase NOx by lengthening the flame and introducing more nitrogen. Though very high excess air may cool the flame and reduce thermal NOx—it’s a balancing act. Low-NOx and ultra-low-NOx burners use specialized combustion heads, staged firing, and flue gas recirculation to reduce emissions.
Burner load matters too. Many burners emit less NOx at high fire, so it may be better to cycle off than idle at low fire. Lead-lag control across multiple boilers can keep one unit running efficiently while others stay off. Modern systems can automate this strategy.
Emissions should be verified during burner tuning and checked regularly. Rising NOx or CO levels may signal worn nozzles, buildup, or control drift.
Burner Tuning And Air-to-Fuel Ratio Control
Burner conditions are never static (boiler loads change, fuel quality varies, air density shifts with weather). This is why maintaining the optimum air-fuel mix requires regular burner tuning. This involves adjusting the burner’s fuel flow and airflow settings so that at each firing rate, the combustion is efficient and clean. A poorly tuned burner can increase fuel consumption, drive up emissions, and shorten boiler life .
What does burner tuning involve? It’s part science, part art and should be done by an experienced technician . Key steps include:
- Inspection: Check the burner and boiler for any mechanical issues – fan obstructions or worn parts that could upset combustion .
- Set and Adjust Air-Fuel Ratio: Using combustion instruments, the technician fine-tunes the burner’s fuel valve and air damper (or fan speed). The goal is to achieve optimal O₂ and CO readings across the firing range. Whether using modern linkage-less controls or older jackshaft systems, adjustments are made at high fire, low fire, and sometimes mid-fire. This is done to create a smooth fuel/air curve. The goal is to maintain a precise air-to-fuel ratio that avoids unburned fuel (too rich) and excess air (too lean).
- Testing: After adjustments, the burner is test-fired. Flue gas measurements for O₂ and CO confirm the results. Acceptable tuning might be, for example, 3% O₂ and trace CO (<50 ppm) at high fire. And maybe 5% O₂ with low CO at low fire. If CO spikes or O₂ falls off at any point, further fine-tuning is needed .
- Repeat regularly: Tuning is not one-and-done. Burners drift over time as components wear or fuel/air conditions change. It’s recommended to perform a boiler tune quarterly for industrial burners in areas with 4 distinct seasons .
Conclusion: Choosing the Right Industrial Burner Pays Long-Term Dividends
Industrial burners are the heart of any boiler system—impacting everything from fuel efficiency and emissions to plant safety and uptime. Whether you’re optimizing an existing unit or selecting a new burner, success starts with understanding core principles. Air-fuel ratio, burner tuning, advanced controls, safety interlocks, and emissions compliance.
With rising fuel costs and stricter environmental regulations, the right industrial burner can deliver major operational and financial returns. Prioritize performance, reliability, and support—not just upfront price. A properly sized, tuned, and controlled burner will lower NOx and CO emissions, cut fuel waste, and improve combustion consistency across your load range.
If you’re evaluating options, don’t go it alone. Work with a qualified industrial burner expert who understands your system and can tailor recommendations to your plant’s needs. The result? Safer operation, higher efficiency, and long-term savings.
Bonus Section: Industrial Burners Applications and Types
Industrial burners are a core component of boiler systems and high-temperature heating processes. They enable precise flame control to generate steam, produce thermal energy, or maintain critical process temperatures. These systems are used across industries such as automotive, food and beverage, power generation, petrochemical, and manufacturing.
Typical industrial burner applications include:
- Heating boiler systems
- Welding and fabrication
- Fluid and liquid heating
- Driving chemical reactions
- Metal melting and recycling
- Glass production and forming
Types
Industrial burners are available in a range of configurations tailored to specific needs:
- Forced Draft Burners (Cold Air Burners): These burners use a blower to deliver combustion air under pressure. They’re standard on many industrial boiler systems and come in various configurations for different fuels and firing rates.
- High-Turndown Burners: Designed for applications with widely varying steam or heat demands, these burners modulate efficiently across a broad range (e.g. 10:1 or higher) to avoid cycling and improve fuel efficiency.
- Low-NOx and Ultra-Low-NOx Burners: Engineered to reduce nitrogen oxide emissions, these burners use staged combustion, flue gas recirculation (FGR), or special flame shaping to stay within regulatory limits—especially important in non-attainment zones or where air permits require <30 ppm NOx.
- Oxy-Fuel Burners: While less common in boilers, these burners use nearly pure oxygen instead of air, resulting in higher flame temperatures and reduced NOx. They’re typically used in high-temperature industrial processes like glass or steel manufacturing.
- Regenerative and Recuperative Burners: Used in process heating applications (not boilers), these designs recover heat from exhaust gases to preheat incoming combustion air—significantly improving system efficiency.
- Package Burners: These all-in-one burners are factory-assembled with integrated blowers, fuel trains, and controls. They simplify installation and are commonly used in retrofits or standardized boiler systems.
- Choosing the right burner type depends on your application, fuel availability, emissions requirements, and boiler design. Understanding these distinctions helps ensure reliable combustion, lower operating costs, and environmental compliance.